Non-Destructive Testing (NDT)
Non-Destructive Testing (NDT), also referred to as Non-Destructive Examination (NDE), is a critical approach for assessing the properties and condition of materials and structures without causing damage. Unlike destructive testing, which renders the tested item unusable, NDT methods preserve the integrity of the equipment, making it a preferred choice across various industries. This technique is essential for identifying discontinuities, flaws, and corrosion in materials, ensuring safety and reliability.
At AIMMS, we provide a broad spectrum of NDT services that include both conventional and advanced methods. Our skilled team utilizes state-of-the-art technologies to deliver precise and dependable results, supporting your operational needs and ensuring regulatory compliance.
INSPECTION SERVICES OVERVIEW
Conventional NDT Methods
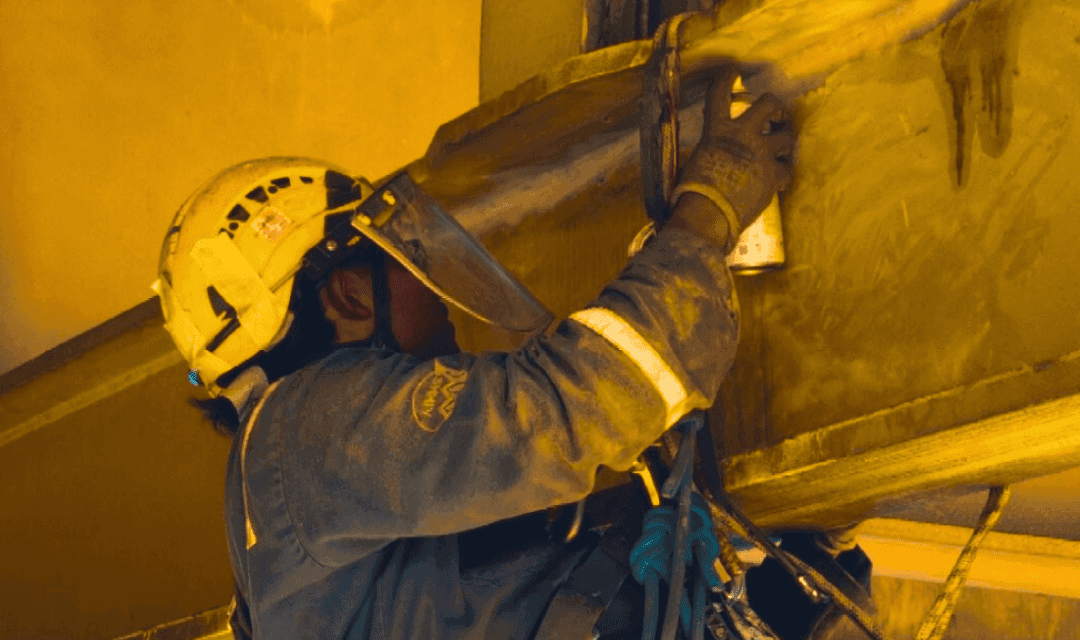
Magnetic Particle Testing (MPT) is designed to detect surface and near-surface discontinuities in ferromagnetic materials. This method involves applying magnetic fields to the material and spreading fine magnetic particles over its surface. These particles accumulate at areas where the magnetic field is disrupted by flaws, making defects visible.
Liquid Penetrant Testing / Dye Penetrant Testing is used to reveal surface-breaking flaws, such as cracks and porosity. It works by applying a liquid dye to the material's surface, which seeps into any cracks or defects. After the dye penetrates, the excess is removed, and a developer is applied to draw the dye out, highlighting the surface flaws.
Ultrasonic Testing (UT) is a method for detecting internal flaws and measuring material thickness. High-frequency sound waves are transmitted into the material, and their reflections from internal discontinuities are captured by a sensor. The time taken for the waves to return helps identify and locate internal defects.
Ultrasonic Thickness Gauging (UTG) is a specialized form of Ultrasonic Testing focused on measuring material thickness with high precision. It uses sound waves to measure the thickness of the material, making it particularly useful for monitoring corrosion and material thinning.
Vacuum Box Leak Testing is employed to detect leaks in welds, seams, and joints. A vacuum box is placed over the area to be tested, and a bubble solution is applied. Leaks are indicated by the appearance of bubbles in the solution as air escapes from the material.
Visual Testing involves directly inspecting surfaces for visible defects. This straightforward method can be performed with the naked eye or enhanced using tools such as magnifying glasses or borescopes, allowing for the identification of surface flaws like cracks, corrosion, or wear.
Advanced NDT Methods
Alternating Current Field Measurement (ACFM) is used to detect and size surface-breaking cracks in metallic components. It involves passing an alternating current through the material to create an electric field. The interaction between this field and surface cracks generates detectable signals, enabling the identification and measurement of the cracks.
Eddy Current Testing (ECT) detects surface and near-surface flaws in conductive materials using electromagnetic induction. Eddy currents are induced in the material with an electromagnetic probe, and variations in these currents caused by discontinuities are analyzed to locate and assess the size of the flaws.
Infrared Thermography is a technique for identifying subsurface defects and thermal inefficiencies. Infrared cameras capture thermal images of the material, revealing temperature differences that indicate underlying issues such as defects or energy losses.
Additional Specialized Services
PRV/PG Inspection Services involve comprehensive testing of Pressure Relief Valves (PRVs) and Pressure Gauges (PGs) to ensure accurate pressure measurement and safe operation. This service verifies that pressure systems function correctly and comply with safety standards.
Offshore PRV/PG Inspection provides specialized inspection services for PRVs and PGs in challenging offshore environments. Tailored techniques address the specific conditions of offshore installations, ensuring the safety and efficiency of pressure systems in these demanding settings.

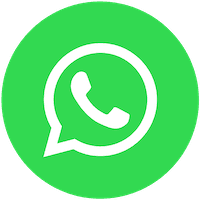
AIMMS Group is a UAE based Marine inspection, maintenance and rope access services provider having delivery centers in India, KSA & UK. Our NDT & UT Gauging team is well versed with oil, gas & marine industries and have delivered services to leading organizations in the sector across the waters. Our rope access based mechanical team is well equipped & skilled to meet corrosion protection, welding , fabrication, painting requirements of any industries.
FOLLOW US
Connect for real-time updates and expert perspectives on industry trends.
HEADQUARTERS
M-35- 16th St, Building 3,
Musaffah,B-2- 18, ICAD, Abu Dhabi, UAE.
PHONE
SERVICES
Copyright © 2024 AIMMS Group. All Rights Reserved.